“Powering Innovation: DC Motors Driving the Future”
Introduction
DC motors, or direct current motors, are widely utilized in various applications due to their simplicity, reliability, and ease of control. These motors convert electrical energy from a direct current source into mechanical energy, making them essential in numerous industries and everyday devices. Common applications include electric vehicles, where they provide efficient and controllable propulsion; industrial machinery, where they drive conveyor belts, cranes, and hoists; and household appliances, such as fans, power tools, and kitchen gadgets. Additionally, DC motors are integral in robotics, offering precise movement control, and in renewable energy systems, where they are used in wind turbines and solar tracking systems. Their versatility and adaptability make DC motors a cornerstone in both consumer and industrial technologies.
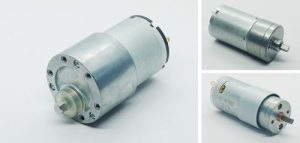
Industrial Automation
DC motors, or direct current motors, play a pivotal role in the realm of industrial automation, offering a versatile and efficient means of converting electrical energy into mechanical motion. These motors are integral to a wide array of applications due to their ability to provide precise control over speed and torque, which are essential parameters in automated systems. The adaptability of DC motors makes them suitable for various industrial tasks, ranging from simple conveyor belt operations to complex robotic systems.
One of the primary advantages of DC motors in industrial automation is their ease of speed control. By adjusting the voltage applied to the motor, operators can fine-tune the motor’s speed to match the specific requirements of the application. This capability is particularly beneficial in processes where varying speeds are necessary, such as in assembly lines where different stages of production may require different operational speeds. Furthermore, the ability to maintain a constant speed under varying loads ensures that production processes remain consistent and reliable.
In addition to speed control, DC motors offer excellent torque characteristics, which are crucial for applications requiring high starting torque or precise torque regulation. For instance, in material handling systems, DC motors can provide the necessary force to move heavy loads from one point to another efficiently. This is achieved through the use of gearboxes and other mechanical components that enhance the motor’s torque output. The precise control over torque also makes DC motors ideal for applications such as robotic arms, where accurate positioning and movement are essential.
Moreover, the simplicity and reliability of DC motors contribute to their widespread use in industrial automation. Unlike their AC counterparts, DC motors have a straightforward design that typically involves fewer components, resulting in lower maintenance requirements and reduced downtime. This reliability is critical in industrial settings where continuous operation is often necessary to meet production targets. Additionally, the robust construction of DC motors allows them to withstand harsh industrial environments, including exposure to dust, moisture, and temperature variations.
Another significant application of DC motors in industrial automation is in the field of automated guided vehicles (AGVs). These vehicles rely on DC motors for propulsion and steering, enabling them to navigate complex factory layouts autonomously. The precise control offered by DC motors ensures that AGVs can move accurately along predetermined paths, avoiding obstacles and ensuring the efficient transport of materials within the facility. This automation not only enhances productivity but also reduces the risk of human error and workplace accidents.
Furthermore, DC motors are extensively used in the automation of packaging machinery. In these applications, the motors drive various components such as conveyor belts, rollers, and cutting mechanisms. The ability to control the speed and torque of these components ensures that packaging processes are carried out with high precision and consistency. This is particularly important in industries such as food and beverage, pharmaceuticals, and consumer goods, where packaging quality directly impacts product integrity and customer satisfaction.
In conclusion, the versatility, precision, and reliability of DC motors make them indispensable in the field of industrial automation. Their ability to provide precise control over speed and torque, coupled with their robust construction and ease of maintenance, ensures that they can meet the demanding requirements of modern industrial processes. As technology continues to advance, the role of DC motors in industrial automation is likely to expand further, driving innovation and efficiency across various sectors.
Electric Vehicles
Electric vehicles (EVs) have emerged as a pivotal technology in the quest for sustainable transportation, and at the heart of many of these vehicles lies the direct current (DC) motor. The application of DC motors in electric vehicles is driven by their efficiency, reliability, and controllability, making them an ideal choice for this innovative mode of transport. Understanding the role of DC motors in EVs requires an exploration of their operational principles, advantages, and specific applications within the vehicle’s architecture.
DC motors operate on the principle of converting electrical energy into mechanical energy through the interaction of magnetic fields. When a current flows through the motor’s windings, it generates a magnetic field that interacts with the field of the permanent magnets or electromagnets within the motor. This interaction produces a torque that drives the motor’s rotor, resulting in rotational motion. The ability to precisely control this motion is one of the key reasons DC motors are favored in electric vehicles.
One of the primary advantages of DC motors in EVs is their high efficiency. Electric vehicles demand efficient energy conversion to maximize the range and performance of the vehicle. DC motors, particularly brushless DC (BLDC) motors, offer high efficiency due to their reduced friction and lower energy losses compared to traditional brushed motors. This efficiency translates to longer driving ranges and lower energy consumption, which are critical factors for the widespread adoption of electric vehicles.
Moreover, DC motors provide excellent torque characteristics, which are essential for the performance of electric vehicles. The torque produced by a DC motor is directly proportional to the current supplied, allowing for precise control over the vehicle’s acceleration and deceleration. This characteristic is particularly beneficial in urban driving conditions, where frequent stops and starts are common. The ability to deliver high torque at low speeds also enhances the vehicle’s performance during hill climbs and other demanding driving scenarios.
In addition to their efficiency and torque capabilities, DC motors offer superior controllability. The speed and direction of a DC motor can be easily controlled by adjusting the voltage and current supplied to the motor. This controllability is crucial for electric vehicles, as it allows for smooth and responsive acceleration, regenerative braking, and efficient energy management. Regenerative braking, in particular, is a significant advantage of DC motors in EVs. During braking, the motor acts as a generator, converting kinetic energy back into electrical energy, which is then stored in the vehicle’s battery. This process not only extends the driving range but also enhances the overall energy efficiency of the vehicle.
The application of DC motors in electric vehicles extends beyond propulsion. They are also used in various auxiliary systems within the vehicle, such as power steering, air conditioning, and cooling systems. These auxiliary systems benefit from the same efficiency, controllability, and reliability that DC motors provide in the propulsion system, contributing to the overall performance and energy efficiency of the vehicle.
In conclusion, the application of DC motors in electric vehicles is a testament to their efficiency, torque characteristics, and controllability. These motors play a crucial role in the propulsion and auxiliary systems of EVs, driving the performance and energy efficiency that are essential for the success of this sustainable transportation technology. As electric vehicles continue to evolve, the role of DC motors will remain integral, underscoring their importance in the future of automotive engineering.
Robotics
DC motors are integral components in the field of robotics, providing the necessary actuation to drive various mechanical systems. Their versatility and efficiency make them suitable for a wide range of applications, from simple hobbyist projects to complex industrial robots. Understanding the specific roles that DC motors play in robotics can offer insights into their importance and the reasons behind their widespread use.
One of the primary applications of DC motors in robotics is in the actuation of wheels and tracks. Mobile robots, whether they are autonomous vehicles or remote-controlled units, rely on DC motors to convert electrical energy into mechanical motion. The ability to precisely control the speed and direction of these motors allows for accurate navigation and maneuverability. This is particularly crucial in environments where precision is paramount, such as in search and rescue missions or in automated guided vehicles (AGVs) used in warehouses.
In addition to locomotion, DC motors are also employed in robotic arms and manipulators. These systems require a high degree of precision and control to perform tasks such as assembly, welding, and material handling. DC motors, often coupled with gearboxes and encoders, provide the necessary torque and feedback to ensure that the robotic arms move accurately and repeatably. The use of pulse-width modulation (PWM) to control the speed and position of these motors further enhances their capability to perform delicate and complex tasks.
Furthermore, DC motors are utilized in the actuation of robotic joints. In humanoid robots, for instance, the joints must mimic the range of motion and flexibility of human limbs. DC motors, with their ability to provide smooth and continuous rotation, are ideal for this purpose. By integrating sensors and control algorithms, these motors can achieve the fine motor control required for tasks such as walking, grasping objects, and even facial expressions.
Another significant application of DC motors in robotics is in the operation of sensors and feedback systems. Many robotic systems rely on a variety of sensors to interact with their environment, including cameras, LIDAR, and ultrasonic sensors. DC motors are often used to pan and tilt these sensors, allowing the robot to gather comprehensive data from its surroundings. This capability is essential for tasks such as object recognition, obstacle avoidance, and environmental mapping.
Moreover, DC motors play a crucial role in the development of robotic exoskeletons. These wearable devices are designed to augment human strength and endurance, providing assistance to individuals with mobility impairments or those engaged in physically demanding tasks. The precise control offered by DC motors enables the exoskeleton to move in harmony with the user’s natural movements, thereby enhancing their capabilities without causing discomfort or strain.
In addition to these applications, DC motors are also found in smaller, specialized robotic systems. For example, micro-robots used in medical applications, such as minimally invasive surgery or targeted drug delivery, rely on miniature DC motors for their actuation. These motors must be highly reliable and efficient, given the critical nature of their tasks and the constraints of operating within the human body.
In conclusion, DC motors are indispensable in the realm of robotics, offering the necessary actuation and control for a wide array of applications. Their ability to provide precise, reliable, and efficient motion makes them a cornerstone of modern robotic systems. As technology continues to advance, the role of DC motors in robotics is likely to expand, driving further innovation and enabling new capabilities in this dynamic field.
Home Appliances
DC motors, or direct current motors, are integral components in a wide array of home appliances, providing the necessary mechanical energy to perform various tasks efficiently. These motors convert electrical energy into mechanical energy through the interaction of magnetic fields, making them highly versatile and reliable for numerous applications. Understanding the role of DC motors in home appliances requires an appreciation of their operational principles, advantages, and specific uses.
One of the primary reasons DC motors are favored in home appliances is their ability to offer precise control over speed and torque. This characteristic is particularly beneficial in devices where variable speed is essential. For instance, in vacuum cleaners, DC motors allow for adjustable suction power, enabling users to clean different surfaces effectively. Similarly, in washing machines, these motors facilitate the regulation of drum speed, ensuring optimal washing cycles for various fabric types. The ability to modulate speed and torque not only enhances performance but also contributes to energy efficiency, a critical consideration in modern household appliances.
Moreover, DC motors are known for their compact size and high power-to-weight ratio, making them ideal for applications where space is a constraint. In kitchen appliances such as blenders and food processors, the compactness of DC motors allows for sleek and ergonomic designs without compromising on power. These motors can deliver high rotational speeds, essential for chopping, blending, and grinding tasks, thereby improving the overall functionality of the appliance. Additionally, the reduced size and weight contribute to the portability and ease of use of these devices, enhancing user convenience.
Another significant advantage of DC motors is their relatively simple construction and ease of maintenance. This simplicity translates to higher reliability and longer operational life, which are crucial factors for home appliances that are used frequently. For example, in electric fans, the straightforward design of DC motors ensures consistent performance with minimal maintenance requirements. The durability of these motors also means that appliances can withstand prolonged usage without significant wear and tear, thereby offering better value for money to consumers.
Furthermore, the quiet operation of DC motors is a notable benefit, especially in household environments where noise levels are a concern. Appliances such as air purifiers and humidifiers, which are often used in living spaces and bedrooms, benefit from the low noise output of DC motors. This quiet operation enhances the comfort and tranquility of the home environment, making these appliances more appealing to users.
In addition to their practical advantages, DC motors also support the growing trend towards smart home technology. Many modern appliances are now equipped with sensors and microcontrollers that require precise motor control for optimal performance. DC motors, with their excellent controllability, are well-suited for integration with these advanced systems. For instance, robotic vacuum cleaners utilize DC motors to navigate and clean homes autonomously, adjusting their speed and direction based on sensor inputs. This integration of DC motors with smart technology not only improves the efficiency of the appliances but also aligns with the increasing demand for automation and convenience in household tasks.
In conclusion, DC motors play a pivotal role in the functionality and efficiency of various home appliances. Their ability to provide precise control, compact size, ease of maintenance, quiet operation, and compatibility with smart technology makes them indispensable in modern households. As technology continues to advance, the applications of DC motors in home appliances are likely to expand further, driving innovation and enhancing the quality of life for users.
Aerospace Systems
DC motors play a pivotal role in aerospace systems, offering a blend of reliability, efficiency, and precision that is crucial for the demanding environment of aviation and space exploration. These motors are integral to various subsystems within aircraft and spacecraft, where their unique characteristics are leveraged to enhance performance and ensure operational success.
One of the primary applications of DC motors in aerospace systems is in the actuation of control surfaces. Control surfaces, such as ailerons, elevators, and rudders, are essential for maneuvering an aircraft. DC motors are employed to drive the actuators that adjust these surfaces, providing the necessary force and precision to maintain stability and control during flight. The ability of DC motors to offer fine-tuned control and rapid response times makes them ideal for this application, where even minor deviations can have significant consequences.
In addition to control surfaces, DC motors are also used in landing gear systems. The deployment and retraction of landing gear require robust and reliable actuation mechanisms. DC motors, with their high torque and dependable performance, are well-suited for this task. They ensure that the landing gear can be extended and retracted smoothly and efficiently, contributing to the safety and reliability of the aircraft during takeoff and landing phases.
Furthermore, DC motors are employed in the operation of various onboard systems, such as pumps and fans. For instance, fuel pumps driven by DC motors are critical for maintaining the flow of fuel to the engines, ensuring consistent and reliable engine performance. Similarly, ventilation and cooling systems within the aircraft cabin and avionics compartments rely on DC motors to drive fans that regulate temperature and airflow. The efficiency and durability of DC motors make them indispensable in these applications, where continuous operation is essential.
In the realm of space exploration, DC motors are equally significant. Spacecraft often utilize DC motors for the deployment of solar panels, antennas, and other extendable structures. The precision and reliability of DC motors are crucial in the vacuum of space, where mechanical failures can jeopardize entire missions. The ability to operate in extreme conditions, coupled with their relatively simple control mechanisms, makes DC motors a preferred choice for space applications.
Moreover, DC motors are integral to robotic systems used in space exploration. Rovers and robotic arms, which are essential for conducting scientific experiments and gathering data on other planets, rely on DC motors for mobility and manipulation tasks. The adaptability and precise control offered by DC motors enable these robotic systems to perform complex operations with high accuracy, thereby expanding the capabilities of space missions.
In conclusion, the applications of DC motors in aerospace systems are vast and varied, encompassing critical functions in both aviation and space exploration. Their reliability, efficiency, and precision make them indispensable components in the actuation of control surfaces, landing gear systems, onboard pumps and fans, and space exploration equipment. As aerospace technology continues to advance, the role of DC motors is likely to expand further, driving innovation and enhancing the performance and safety of aerospace systems. The seamless integration of DC motors into these systems underscores their importance and highlights their contribution to the progress of aerospace engineering.
Q&R
1. **What is a common application of DC motors in household appliances?**
– DC motors are commonly used in household appliances such as vacuum cleaners and electric shavers.
2. **How are DC motors utilized in the automotive industry?**
– In the automotive industry, DC motors are used in applications like windshield wipers, power windows, and seat adjustments.
3. **What role do DC motors play in robotics?**
– DC motors are essential in robotics for driving wheels, actuating arms, and controlling various robotic movements.
4. **Why are DC motors preferred in portable electronic devices?**
– DC motors are preferred in portable electronic devices like laptops and smartphones for their compact size and efficient power consumption.
5. **How are DC motors used in industrial automation?**
– In industrial automation, DC motors are used in conveyor belts, robotic arms, and other machinery requiring precise speed and position control.
Conclusion
DC motors are widely used in various applications due to their simplicity, ease of control, and reliability. They are commonly found in household appliances, automotive systems, industrial machinery, and robotics. Their ability to provide precise speed and torque control makes them ideal for applications requiring variable speed and load conditions. Additionally, advancements in power electronics and control systems have further enhanced the efficiency and performance of DC motors, solidifying their role in modern technology.